Posts Tagged ‘reverse mcu file’
Reverse Chip PIC12LC508 Heximal File
Reverse Chip PIC12LC508 Heximal File is a process to replicate cpu pic12lf508 program from memory, and then extract the code from pic12lf508 locked flash memory.
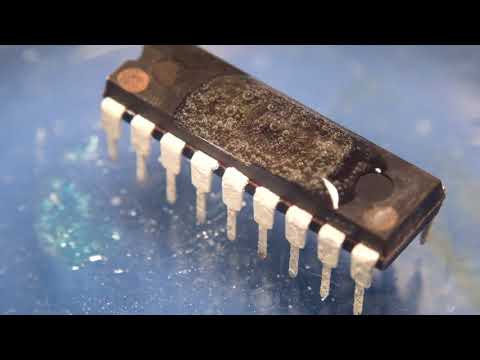
A serial frame for the MSPIM is defined to be one character of 8 data bits. The USART in MSPIM mode has two valid frame formats:
8-bit data with MSB first
8-bit data with LSB first
A frame starts with the least or most significant data bit. Then the next data bits, up to a total of eight, are succeeding, ending with the most or least significant bit accordingly when attack mcu aduc831bsz firmware Heximal file.
When a complete frame is transmitted, a new frame can directly follow it, or the communication line can be set to an idle (high) state.
The UDORDn bit in UCSRnC sets the frame format used by the USART in MSPIM mode. The Receiver and Transmitter use the same setting. Note that changing the setting of any of these bits will corrupt all ongoing communication for both the Receiver and Transmitter before attack mcu tms320f28027pta CHIP.
16-bit data transfer can be achieved by writing two data bytes to UDRn. A UART transmit complete interrupt will then signal that the 16-bit value has been shifted out.
The USART in MSPIM mode has to be initialized before any communication can take place. The initialization process normally consists of setting the baud rate, setting master mode of operation (by setting DDR_XCKn to one), setting frame format and enabling the Transmitter and the Receiver.
Only the transmitter can operate independently. For interrupt driven USART operation, the Global Interrupt Flag should be cleared (and thus interrupts globally disabled) when doing the initialization.
Note:
To ensure immediate initialization of the XCKn output the baud-rate register (UBRRn) must be zero at the time the transmitter is enabled.
Contrary to the normal mode USART operation the UBRRn must then be written to the desired value after the transmitter is enabled, but before the first transmission is started after copy pic16lf877 program.
Setting UBRRn to zero before enabling the transmitter is not necessary if the initialization is done immediately after a reset since UBRRn is reset to zero.
Before doing a re-initialization with changed baud rate, data mode, or frame format, be sure that there is no ongoing transmissions during the period the registers are changed if copy mcu pic18f2480 program.
The TXCn Flag can be used to check that the Transmitter has completed all transfers, and the RXCn Flag can be used to check that there are no unread data in the receive buffer.
Note that the TXCn Flag must be cleared before each transmission (before UDRn is written) if it is used for this purpose. The following simple USART initialization heximal file examples show one assembly and one C function that are equal in functionality.
The examples assume polling (no interrupts enabled). The baud rate is given as a function parameter. For the assembly heximal file, the baud rate parameter is assumed to be stored in the r17:r16 registers.
Reverse MCU ATmega461PV Binary
Reverse MCU ATmega461PV and readout microcontroller atmega461pv secured Binary, crack mcu protective system and using focus ion beam to cut off the security fuse bit;
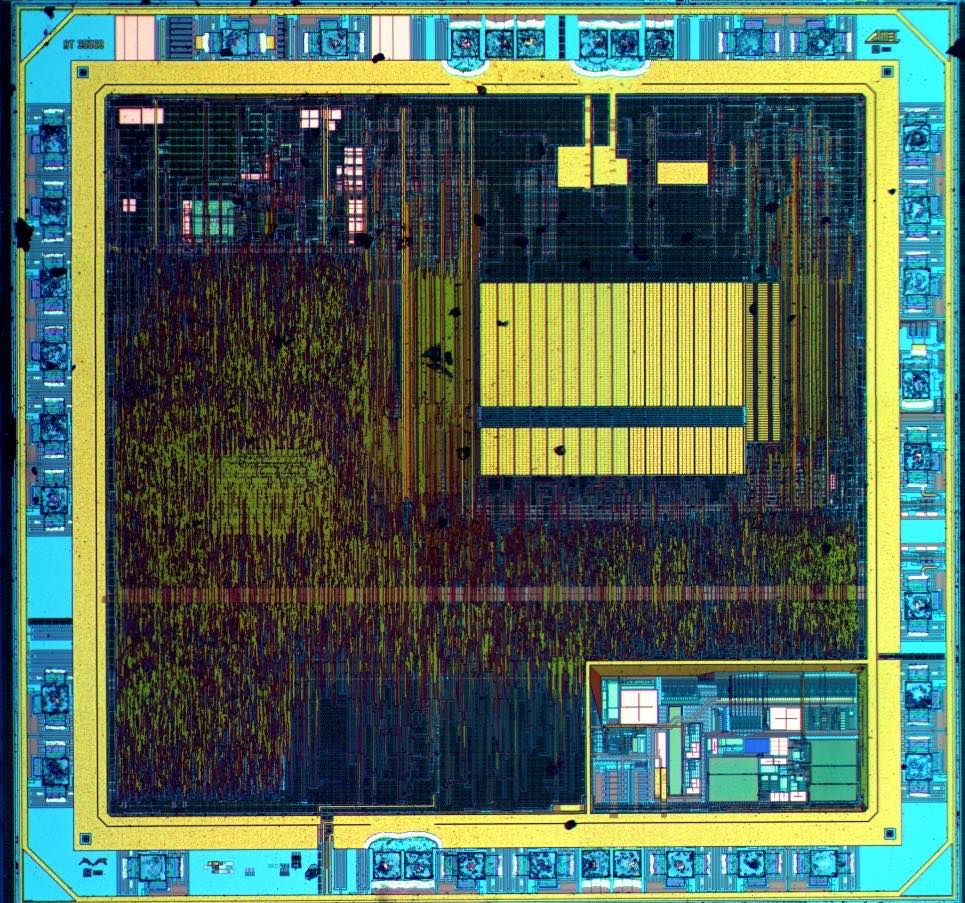
The interconnection between Master and Slave CPUs with SPI is shown in Figure 80. The system consists of two shift Registers, and a Master clock generator. Th e SPI Master initiates the communication cycle when pulling low the Slave Select SS pin of the desired Slave.
Master and Slave prepare the data to be sent in their respective shift Registers, and the Master generates the required clock pulses on the SCK line to interchange data if break atmega64pa MCU binary.
Data is always shifted from Master to Slave on the Master Out – Slave In, MOSI, line, and from Slave to Master on the Master In – Slave Out, MISO, line. After each data packet, the Master will synchronize the Slave by pulling high the Slave Select, SS, line.
When configured as a Master, the SPI interface has no automatic control of the SS line. This must be handled by user software before communication can start. When this is done, writing a byte to the SPI Data Register starts the SPI clock generator, and the hardware shifts the eight bits into the Slave. After shifting one byte, the SPI clock generator stops, setting the end of Transmission Flag (SPIF) after break atmega128a MCU firmware.
If the SPI Interrupt Enable bit (SPIE) in the SPCR Register is set, an interrupt is requested. The Master may continue to shift the next byte by writing it into SPDR, or signal the end of packet by pulling high the Slave Select, SS line. The last incoming byte will be kept in the Buffer Register for later use. When configured as a Slave, the SPI interface will remain sleeping with MISO tri-stated as long as the SS pin is driven high. In this state, software may update the contents of the SPI Data Register, SPDR, bu t the data will not be shifted out by incoming clock pulses on the SCK pin until the SS pin is driven low.
As one byte has been completely shifted, the end of Transmission Flag, SPIF is set. If the SPI Interrupt Enable bit, SPIE, in the SPCR Register is set, an interrupt is requested.
The Slave may continue to place new data to be sent into SPDR before reverseing the incoming data. The last incoming byte will be kept in the Buffer Register for later use. The system is single buffered in the transmit direction and double buffered in the receive direction. This means that bytes to be transmitted cannot be written to the SPI Data Register before the entire shift cycle is completed.
When receiving data, however, a received character must be reverse from the SPI Data Register before the next character has been completely shifted in. Otherwise, the first byte is lost.
In SPI Slave mode, the control logic will sample the incoming signal of the SCK pin. To ensure correct sampling of the clock signal, the frequency of the SPI clock should never exceed fosc/4.
Reverse MCU ATMEGA261 Heximal
We can Reverse Mcu ATMEGA261 Heximal, please view the Mcu ATMEGA261 features for your reference:
The N variable represents the prescale factor (1, 8, 32, 64, 128, 256, or 1024). The extreme values for the OCR2A Register represent special cases when generating a PWM waveform output in the fast PWM mode.
If the OCR2A is set equal to BOTTOM, the output will be a narrow spike for each MAX+1 timer clock cycle. Setting the OCR2A equal to MAX will result in a constantly high or low output (depending on the polarity of the output set by the COM2A1:0 bits.) when Reverse Mcu Heximal.
A frequency (with 50% duty cycle) waveform output in fast PWM mode can be achieved by setting OC2x to toggle its logical level on each compare match (COM2x1:0 = 1). The waveform generated will have a maximum frequency of foc2 = fclk_I/O/2 when OCR2A is set to zero if Reverse Mcu Heximal.
This feature is similar to the OC2A toggle in CTC mode, except the double buffer feature of the Output Compare unit is enabled in the fast PWM mode. The phase correct PWM mode (WGM22:0 = 1 or 5) provides a high resolution phase correct PWM waveform generation option before Reverse Mcu Heximal.
The phase correct PWM mode is based on a dual-slope operation. The counter counts repeatedly from BOTTOM to TOP and then from TOP to BOTTOM. TOP is defined as 0xFF when WGM22:0 = 1, and OCR2A when MGM22:0 = 5. In non-inverting Compare Output mode, the Output Compare (OC2x) is cleared on the compare match between TCNT2 and OCR2x while upcounting, and set on the compare match while downcounting after Reverse Mcu Heximal.
In inverting Output Compare mode, the operation is inverted. The dual-slope operation has lower maximum operation frequency than single slope operation. However, due to the symmetric feature of the dual-slope PWM modes, these modes are preferred for motor control applications if Reverse Mcu Heximal.
In phase correct PWM mode the counter is incremented until the counter value matches TOP. When the counter reaches TOP, it changes the count direction. The TCNT2 value will be equal to TOP for one timer clock cycle. The timing diagram for the phase correct PWM mode is shown on Figure 73 before Reverse Mcu Heximal.
The TCNT2 value is in the timing diagram shown as a histogram for illustrating the dual-slope operation. The diagram includes non-inverted and inverted PWM outputs. The small horizontal line marks on the TCNT2 slopes represent compare matches between OCR2x and TCNT2 when Reverse Mcu Heximal.
The Timer/Counter Overflow Flag (TOV2) is set each time the counter reaches BOTTOM. The Interrupt Flag can be used to generate an interrupt each time the counter reaches the BOTTOM value. In phase correct PWM mode, the compare unit allows generation of PWM waveforms on the OC2x pin. Setting the COM2x1:0 bits to two will produce a non-inverted PWM. An inverted PWM output can be generated by setting the COM2x1:0 to three. TOP is defined as 0xFF when WGM2:0 = 3, and OCR2A when MGM2:0 = 7 (See Table 87 on page 185). The actual OC2x value will only be visible on the port pin if the data direction for the port pin is set as output if Reverse Mcu Heximal.
The PWM waveform is generated by clearing (or setting) the OC2x Register at the compare match between OCR2x and TCNT2 when the counter increments, and setting (or clearing) the OC2x Register at compare match between OCR2x and TCNT2 when the counter decrements. The PWM frequency for the output when using phase correct PWM can be calculated by the following equation.